
Access Control

Asset and Inventory Management
Twenteborg Hospital implements bed management system
by Roland Stump, Dorset b.v.
Twenteborg Hospital in Almelo, Netherlands, has implemented a full bed management system based on the ID200 transponder. An ID200 tag was attached to each bed in the same relative position. This tag is scanned once the bed goes from the dirty to the clean room. The ID number is transmitted to the central computer that looks up whether maintenance should be performed. In the affirmative case, a light will illuminate and a report on the items to check comes prints automatically.
Once the bed is cleaned and properly made, it goes into stock. Nurses can collect a bed with a simple check-out procedure: scanning it and then scanning the transponder identifying the department to which they will take it. An ANT-611 sensor antenna is used for the check out.
The hospital’s objective is to document that the manufacturer’s maintenance schedule has been properly followed. Also, individual departments can be charged for the number of beds used and a better overview on the status and use of the beds can be obtained.
An ANT-614 antenna for reading the beds was placed inside the washing machine. Water, chemicals, and temperature have no effect on the reading.

Automotive manufacture (production control)
Building cars a better way at Opel
by Gerhard Timme, Euro Identifikationssysteme GmbH
The Opel Corporation has implemented the TROVAN RFID system in its German chassis production plant in order to monitor product quality and introduce process efficiencies. The application is an example of successful implementation of the TROVAN system under marginal and difficult environmental conditions.
The Opel Manufacturing Plant in which the TROVAN system is being implemented is one of the largest automotive plants in Europe. Two parallel assembly lines manufacture about 1,600 vehicles per day., The production lines are not dedicated lines for a single model only. Rather, both production lines assemble Astra and Vectra model automobiles, as well as left and right hand drive vehicles in a mixed fashion. As a result, there is an optimal use of the capital equipment in the plant, but the flip side is that a very well-developed production control system must be in place in order to ensure that the correct parts are assembled in the correct chassis.
The dashboard modules are introduced to the assembly line via a single (gondola-type) conveyor system. On these product carriers (red gondolas), the respective parts are attached (blue construction). They look quite similar but differ according to the vehicle model for which they are destined by their finish and also according to the requirements of the individual countries to which the vehicles will be shipped. Visual differentiation is quite difficult.
To ensure positive identification in this industrial environment, Opel has conducted exhaustive tests with a variety of identification system and ultimately decided to use the TROVAN passive transponder system. Opel selected the TROVAN system because of its superior environmental and performance characteristics: specifically, the compact yet extremely rugged design of the transponders and the industrial-grade execution of the reader systems and because TROVAN’s unique PSK (phase shift keying) half-frequency transmission technology results in unmatched reliability and a system that is able to function even in areas of extremely high EMI.
Even though the transponder is mounted directly on metal and the readers are located in close proximity to assembly line areas where soldering takes place, positive identification (greater than 99.9%) is guaranteed at a read range of more than 10 cm, while the assembly line is in continuous motion.
The tests conducted in the plant showed that even if the walkie-talkie and RF communication systems being used in the plant were directed to transmit directly at the reader (the antenna of a mobile transmitter was held directly next to the EUR-3020 panel antenna) 100% of the transponder ID codes were read. Use of the TROVAN transponder system ensures that the correct trolley with the correct parts are at the right place at the right time. Thee use of incorrect parts is eliminated. The result is a zero error system which is a significant improvement over earlier quality control solutions. Problem-free assembly of the vehicles is assured. There is no down-time and no time is lost in re-tooling assembly lines to accommodate other vehicle models. As a result, the throughput of the assembly line is improved. The system functions even in the most electro-magnetically challenging environment with no error.

Child safety
KiddyKoral provides safety for children at day care centers and kindergartens
By Mark Cowley, Infotronics International Inc.
At Mount Zion Lutheran School in Boulder, Colorado, security has gone high tech. “People want security for their children,” said Mark Cowley, President of Boulder-based, Infotronics International. "They want to know that they are in a safe environment." Mark Cowley is the parent of two Mount Zion students.
The system incorporates a digital camera and TROVAN passive transponder technology to provide the school with a very flexible access control system and automated accounting system, while controlling movement of the children. Digital photographs of each child and parent(s) are taken and stored in a database along with important emergency contact and medical information for each student. All authorized care givers must be registered in the database and their data is linked to the child’s record via a unique TROVAN ID card. Teachers have quick access to photographs, family contacts and detailed information about each student, including immunizations and allergies. “We have instant access to vital information in emergency situations,” said Cheryl Crabbs, a teacher at Mount Zion. “For new teachers who haven’t yet met all the parents, there’s a picture on there [in the system] so they can make sure it’s the right parent, even if the person doesn’t have a card.”
The first line of defense begins at the door, the only direct entrance into the daycare center. Parents have specially coded cards that are scanned to open the lock of the door. Parents are pleased with the system. “I like that it’s convenient and quick,” says Jennifer Turner, a parent. Once inside parents scan the card again at a PC, where they can check their children in and out of daycare. The system keeps track of who dropped off and picked up which children at what time, down to the minute. When the child is picked up, the ID card is scanned and the photographs of the children linked to that card are displayed for the operator to authorize release.
KiddyKoral automatically captures drop-off and pickup times for billing calculations and provides a number of reports to aid in facility administration, invoicing and tracking of payments and receipts.

Companion Animal Recovery
Bruce's adventure in the UK
A dog’s TROVAN microchip helps bring him home
Emailed to Central Animal Records, Australia - 27 February 2006
Bruce, our 16 and half year old Border Collie cross, decided to go on an adventure last Monday and it wasn't until 7:30 pm at night, after we returned home from work, that we realised he had gone. Kirstie, our daughter, said that she had seen him in the yard at about 4 pm so we hoped that he hadn't gone too far. But, we were concerned because we now live in the Surrey, England and being winter over here it gets dark at around 6 pm. The temperature was close to zero, we have a river behind us and many ditches full of water in the wooded common in front of us. Beyond that, was a major road.
We had been in the UK for a number of years now and every morning I take Bruce for a walk in the wooded common out front. We meander down the path and it doesn't take long before he is worn out and ready to shuffle home. Every evening we hear him sniffing at the gate when we pull up in the driveway, he is happy that we are home. So on Monday evening, we were surprised that we could not hear him sniffing and a quick check of his bed revealed he was not their either. We checked the rest of the yard but he was nowhere to be found and there was no obvious signs of a break out. This concerned us because he now suffers from arthritis and becomes disorientated when he is in unfamiliar surroundings. He no longer has the strength to push open gates or squeeze through small holes in the fence.
Knowing that we had not seen him on our drive home, we knew that he had not been run over. Our real concern was that he may have fallen down one of the ditches in the wooded common and became stranded, cold and wet. So we rounded up the family, donned our winter jackets, grabbed our powerful torch and went looking for him. We checked everywhere but to no avail and our neighbours hadn't seen him either. So, forlornly we all went home wondering whether poor Bruce would be spending the night in the wet and cold.
At 4 am Tuesday morning we received a phone call from our parents in Australia letting us know that Bruce had been found, he was safe and sound in the pound. We were relieved that he was okay. Apparantly, he had been wandering in the middle of the busy road, all confused and disorientated when 2 ladies picked him up and took him to our local vets. Unfortunately, although Bruce was wearing a collar, he didn't have a dog tag so the vets checked for a micro chip. And, yes, they found he had one but it was not a recognised UK micro chip.
So, they contacted the UK micro chipping company, Pet Detect, who recognised it was a Trovan chip and sent an email to Central Animal Records (CAR) in Australia. Bev Taylor of CAR checked their records and phoned our parents, living in Gisborne, who we had registered as alternative contacts. So, with Bev's help we had found Bruce. As soon as the pound opened on Tuesday morning, we were there to pick him up. Happy that he was warm, safe and sound and happy to have him home again. We still aren't sure how he got out but we think the catch on the gate is faulty and we now keep the gate bolted.
We are so happy we had him micro chipped before we left Australia and, with today's communication technology, we were contacted from the other side of the world within 12 hours of him going missing from home. We are now making enquiries to get his micro chip details updated so that they have a record of him in the UK - you may not be able to teach an old dogs new tricks but he has certainly taught us ...
We would like to thank Bev very much for helping us to get him back so quickly.
From
Anita Kim
(Guildford, Surrey, United Kingdom)

Fisheries Management

Garment tracking and sorting

Gas cylinder tracking
Welding Distributor Implements “Star Wars” Technology to track gas cylinders
By Jim Broughton, Dataweld Inc.
Coastal Welding Supply of Beaumont, Texas, has become one of the first welding supply distributors in the nation to implement what some would consider “Star Wars” technology to track their compressed gas cylinders. At the heart of Coastal’s new system is a high tech radio frequency identification tag. This tag, also known as a transponder, plus new sophisticated software has given Coastal the ability to track their cylinders with greater accuracy than was previously possible.
According to Coastal Vice President, Chuck Mazock, “We were not pleased with the durability of the barcodes we were using and our old cylinder tracking software was no longer being supported. We had heard about transponder technology and since we are a Praxair distributor we called them for guidance. Praxair had just completed a successful pilot test of TROVAN transponder in Brazil. The test showed that the TROVAN transponder was very durable.”
When questioned about the durability of the transponder, Trovan explained some of the tests the transponder has successfully passed. The tests included: repeated shot blasting, heated to 300 degrees Fahrenheit for 30 minutes, dropped into liquid nitrogen, exposed to high doses of radiation and subjected to 100,000 volts of electricity.
One of the requirements of the Praxair pilot project was for the transponder to not be visible but still be readable. A hole was drilled in the neck ring, the transponder inserted, covered with epoxy and then painted over. Even under these conditions the transponder could easily be read. In fact, according to Trovan, Ltd., their transponder can be read through ice, snow, paint, mud, grease, wood, plastic or cement.
To complete the upgrades of his cylinder tracking system, Mazock also installed AcuTrax, a cylinder tracking system developed by Dataweld of Bossier City, Louisiana. Two features that caught hiseye were Dataweld’s portable database and their open system concept.
“We had significant investment in our account system and did not want to replace it.” reports Mazock. According to Dataweld, the open system design of AcuTrax allows distributors to install the cylinder tracking system without having to replace their existing accounting software.
The portable database offered by AcuTrax allows all transactions captured in the field to be immediately verified. Mazock explains, “When we scan a cylinder in the field the portable database tells us the contents of the cylinder. This eliminates keystrokes for the driver and improves accuracy. AcuTrax also knows where the cylinder should be located. The feature alerts us immediately if a customer returne the cylinder we did not ship them.”
With a year of experience under his belt, Mazock is pleased with the new technology. “Our plans for the coming year are to continue putting transponders on our cylinders and expand the program to our other branch locations.”
In closing, Mazock said, “We feel the durability of the transponder and the upgrades of our tracking system has helped us to minimize cylinder balance discrepancies. After all, our customers deserve our best efforts when it comes to ensuring the accuracy of our cylinder records.“

Guard patrol monitoring

Human health records monitoring and medical research

Beverage keg tracking
Coca Cola: Cost containment and efficiency improvement in keg tracking
When Coca Cola's bottler Rhein-Main-Sieg Getränke GmbH & Co. in Liederbach, Germany modernized its plant, it implemented an automated keg-tracking system based on the trovan® passive transponder system.
The company needed an automated keg-tracking system to improve its process control and plant efficiency. In the old system about 300 kegs per year were subject to forced retirement because of previously unidentified defects, and resulting customer service issues had to be resolved by the bottler's service personnel at customer sites. The plant has 230,000 kegs in circulation and can fill up to 800 kegs every hour.
First the company implemented a barcode system, but the limitations of the technology soon became apparent: the tag has a limited life-span because it eventually peels off or wears down; it requires line-of-sight scanning, thereby reducing the speed of a keg on the conveyor belt; and, finally, the code of the tag, mere ink on paper, can be duplicated.
The solution to the problems was the trovan® passive transponder system, available in North America through Electronic Identification Devices, Ltd. The trovan® transponder consists of an I.C. with a copper antenna coil. It is encapsulated in a ruggedized housing and is the size of a subway token. The microchip is encoded with a unique, tamper-proof code and it does not rely on an internal power source. When a reader passes over the transponder, the transponder emits its code back to the reader where it is displayed on an LCD. The reader is equipped with an RS 232 interface which downloads data to and uploads directives from computers.
"Because of the microchips, every keg can be positively identified, each with its own identification number and its own recorded history," said Karl-Heinz Porsch. The keg history includes data on the age of the container, the number of times it has circulated, and the length of time it has remained with each customer, as well as its contents. With this close monitoring system, the Liederbach plant saved money by reducing the number of kegs needed. It eliminated problem kegs and is keeping more of its keg inventory in circulation at all times. Operational efficiency in the plant itself also increased, since the transponders are permanent and do not require line-of-sight scanning.
The transponders are either epoxied on top of the keg or countersunk in the walls and then sealed. Readers are stationed below the conveyor. When the kegs pass through the production line, they go through eight different checkpoints for cleaning, damage verification, quantity and content control.
Thanks to its new keg tracking system the company has been able to implement a fully automated cleaning station, damage verification station and at the end of the line a quantity and content control station. If something goes wrong with any particular container, the computer-controlled system simply denies the necessary codification and the keg is automatically removed from further processing on the conveyor.
"It is not possible to fool the system. If the conveyor stops, the cause must be resolved before the container is again accepted by the system control of the conveyor," said Managing Director of the bottling company, Erhard Koczorek.
The next stage of implementation closes the logistical gap between the bottler and the customer. "Every delivery driver can add data to each keg's record at the customer site. For instance, date and time of a delivery of pickup," according to Karl Heinz Porsch, representative for AEG Industrial Systems, the systems integrator.
While out in the field, drivers who deposit the kegs at various locations can use hand-held readers to scan customer details and check the status of the kegs. Customers are pleased because the automatic verification feature inherent in the transponder system ensures that they will receive the soft-drink they have ordered in a well-maintained and sterilized keg. In light of the fact that Coca-cola has introduced the use of "on-tap" kegs for soft-drinks to the food-services sector, the number of circulating kegs in the field will grow. Cost contaiment for the existing soft-drink keg stock will remain an important issue. RF/ID has provided the solution.
Managing Director Koczorek agrees with a smile. "I was correct in my judgment call. We have realized tremendous savings from the elimination of problem containers, and customer complaints have been reduced to nearly zero. We feel confirmed in our decision especially when experts from around the world regularly come here to admire our microchip system."

Livestock management
Argentina ranch identifies 35,000 animals with TROVAN transponders for brucellosis eradication
At the Campo General Avalos Ranch, a ranching operation in the Argentinean province of Corrientes, the Instituto Rosenbusch has implemented a comprehensive cattle identification and management program. The ranch is a largescale operation encompassing 37,513 hectares.
More than 35,000 head of cattle were identified with the TROVAN ID-100A transponder, allowing the management to automate herd management and ensure the traceability of individual animals. The GR-100 GRIP™ Computer is being used in conjunction with application-specific software. In certain instances, LID-500 Hand Held Readers are used for back-up.
Electronic ID allows faster processing of animals, resulting in less stress to the animal and in time savings to ranch personnel. It also plays an important part in the brucellosis eradication campaign. Use of unique TROVAN ID codes to identify individual animals in conjunction with rigorous, automated record keeping will allow the operation to be declared free of brucellosis in less than one year.

Ski lift ticketing

Tool tracking
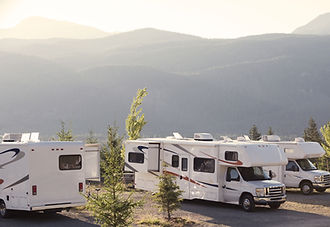
Valuable items registration and insurance
Stoftheft® camper and caravan ID system catches thieves cold
by Douglas McCartney, Identify UK
In eight short weeks of operation, a ground-breaking system has shown itself to be a serious menace to the profit margins and prospects of caravan thieves: caravan and camper owners have begun installing Identify UK’s stoptheft® system, which has already resulted in the recovery of two stolen caravans worth around £30,000. "Effective, permanent identification plays a key role in combating caravan crime," said Chris Nettleton, Development Manager at Caravan Guard, one of the UK’s leading caravan insurers. "We believe the stoptheft®system fulfils that role and have adopted its implementation throughout our customer base."
Historically, recovery of stolen caravans and campers has often proved to be a daunting task. Inspector Geoff Robinson, of the Thames Valley Police Force Traveller Management Unit, explains the police force's predicament: "Police officers face a number of obstacles when attempting to establish the rightful ownership of a suspected stolen caravan. Although all caravans are manufactured with chassis plates and serial numbers, these are easily removed. Criminal law requires the police to prove that an item is stolen to support proceedings against the offending parties and to give the Court a power of confiscation. In the absence of these physically identifiable plates and numbers, many cases are lost. The decision to seize a caravan for closer examination resulting from its lack of a chassis plate or serial number is not one that can be taken lightly, especially if it results in the current occupants being made homeless."
Now, help is on the way for caravan owners and the police officials who have to walk a fine line between protecting the rights of victims and those of individuals suspected of holding stolen vehicles. The solution? The stoptheft® caravan identification and recovery system. The system takes an innovative approach: uniquely coded radio-frequency ID tags are mounted at the front or rear of each caravan. Each ID tag contains a microchip pre-programmed with a unique ID code number, making it impossible for thieves to "crack", duplicate or tamper with the code. A policeman or insurance agent can detect the tag by simply passing a reader over it, at a distance, then check with the national stoptheft® registry to determine the ownership of the vehicle. For added security, additional transponders are hidden in random locations within the interior and/or exterior of the vehicle. The presence of these randomly fitted transponders not only deters theft by increasing risk of prosecution but also reduces the resale value of stolen vans below levels acceptable to professional caravan thieves.
Inspector Robinson explains: "An effective RFID-based system backed up by a national infrastructure of tag readers and a police accessible database removes these problems, enabling officers to establish the identity and thereby the lawful ownership of a caravan quickly and accurately without the need for seizure or vehicle examination. The technology makes the identification of stolen caravans much more efficient and effective and will undoubtably lead to an increase in the number of stolen caravans recovered."
The stoptheft® system is supported nationwide by an infrastructure of tag readers with police, insurance agents and caravan dealerships. Almost 3,500 TROVAN® readers are in police use and today more valuables are fitted with TROVAN® tags in the UK than any other tagging system.
"The TROVAN® system provides absolute ID code uniqueness, meaning that not only does the manufacturer ensure it makes no duplicate ID codes or custom-coded ID codes, but the patented protocol allows legal prosecution of third-party manufacturers of cloned ID codes. This ID code uniqueness is absolutely crucial to establish positive identification of a vehicle and its owner, which is why we have selected this technology over the others." explanied Mr. Nettleton. The tags can be read through most materials, and at any angle.
In March of this year, Identify UK obtained THATCHAM Q listing for its "owner and police friendly" caravan identification system. Thatcham is a world leader in independent vehicle security testing. Its test regime, considered one of the most rigorous in the world, assessed stoptheft®’s performance on several levels; via an on-vehicle test programme, via an evaluation of stoptheft®‘s property register operational procedures and police liaison. The results showed that the system performs as claimed, and demonstrated its reliability, durability and loss-reduction potential in accordance with Thatcham’s requirements for the ‘Q’ Class System Listing.
For the on-vehicle tests, TROVAN® electronic ID tags were randomly embedded into a caravan. A physical inspection failed to reveal the embedded tags. Next, the speed and ease of verifying vehicle identification was assessed. An engineer, with no prior experience of using the TROVAN® LID-500 hand held reader, was able to read the secreted tags, enabling positive identification of the caravan from the stoptheft® property register database.
"The independent testing and evaluation conducted by Thatcham will help to instill confidence within the industry that there is, at last, an effective solution to caravan theft," said Mr. Nettleton.
As a result of the successful Thatcham test, Barron group, the UK’s largest caravan retail group, has implemented the stoptheft® system into all 2002 tourers, campers and motorhomes. Three Trovan transponders are randomly installed, supported by external warning labels and visible ID labels. David Hold, Chief Executive of the Barron Group, explained the company’s decision. "Caravan theft is an increasingly real and frightening issue. We want to prove our commitment to customers’ security by fitting stoptheft® to every single new model that is sold at our Barrons dealerships in Lancashire, Cumbria and Co Durham. Achieving Thatcham listing for the stoptheft® product is a major development in caravan security. Electronic tagging has proved successful as a major theft deterrent in the motor vehicle industry and we believe it will do the same for the caravan industry." The stoptheft® system has already been implemented by German manufacturers, Hobby Fendt for all UK-destined 2002 models. Leading UK insurers and dealers are also backing the technology.
Identify UK, which is promoting the stoptheft® system, is working closely with UK police forces and caravan insurers in order to bring the benefits of the system to caravan owners. Insurers are being offered the product at special prices for volume tagging applications. Comments Identify UK chairman Lord Nicholas Hillsborough, "Caravan owners installing the stoptheft“ electronic tagging kit can rest assured that they are using cutting edge technology from a world leader in electronic identification systems. For those who handle stolen vans to be convinced that the caravan is ‘clean’, the thief would have to locate and remove all the tags randomly fixed or embedded around the caravan, a virtually impossible task making stoptheft“ a tremendous deterrent."
Inspector Robinson sees potential for the technology in a broad spectrum of applications, limited not only to caravans and campers: "Due to the size of RFID transponders, the benefits and protection afforded to caravans is also available to a wide range of other high theft risk property."

Warehouse/stock handling
◄
1 / 1
►